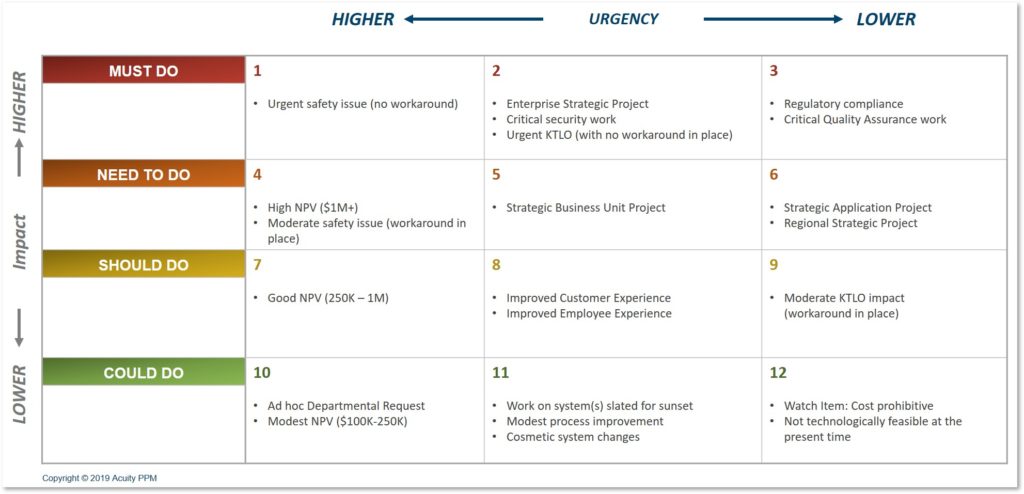
There are many ways to measure the role of waste management in energy conservation. It can be measured in greenhouse gases emissions reduction, carbon neutrality or cost savings. Or it can be used to recover resources. It can also help to create jobs and generate revenue. Also, waste recycling can be a great way to reduce the amount that society produces.
Reduced greenhouse gas emissions
There are many approaches to reduce greenhouse gas emission from waste management. The first is to reduce waste at its source. But, this strategy is not always efficient. It can sometimes even lead to additional GHG emissions. Reduce waste in landfills is another option.
Recycling can decrease greenhouse gas emissions depending upon how the waste is managed. Recycling food scraps, for example, can reduce the amount of waste going to landfill. This will reduce methane emissions from landfills.
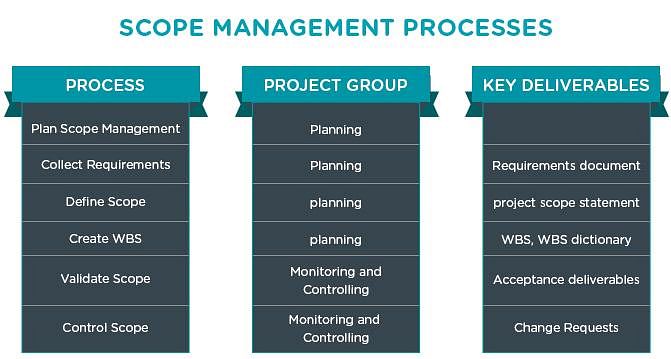
Carbon neutrality
To achieve carbon neutrality, we must reduce carbon emissions while maintaining a stable climate in the future. It offers many benefits to the economy, society and environment. It is an essential goal for many countries today. It will eventually lead to a stable and prosperous society while also reversing the effects of environmental degradation. It will also encourage a shift towards economic development and energy consumption patterns.
Carbon neutrality requires that we move away from fossil fuels to renewable energy. Carbon neutrality is motivated not by technological advances but by increased living standards. To make the transition to renewable energy affordable and sustainable, governments need to work to develop innovative low-carbon technologies. It is important to establish carbon pricing to encourage research and develop to support the transition.
Cost savings
It is important to manage waste. It involves reducing both the amount and type of waste created as well as the material used in its creation. Emissions from the use of natural resource are also reduced by reducing waste. To maximize savings, it is crucial to keep track of all waste produced and to manage it responsibly.
Reducing the production of waste is one of the most effective ways to reduce disposal costs. It is possible to reduce waste by upto half the cost of disposal. Reusing existing products is the most efficient way to reduce trash. Instead of buying a new product, cleaning and repairing used items can save energy and money.
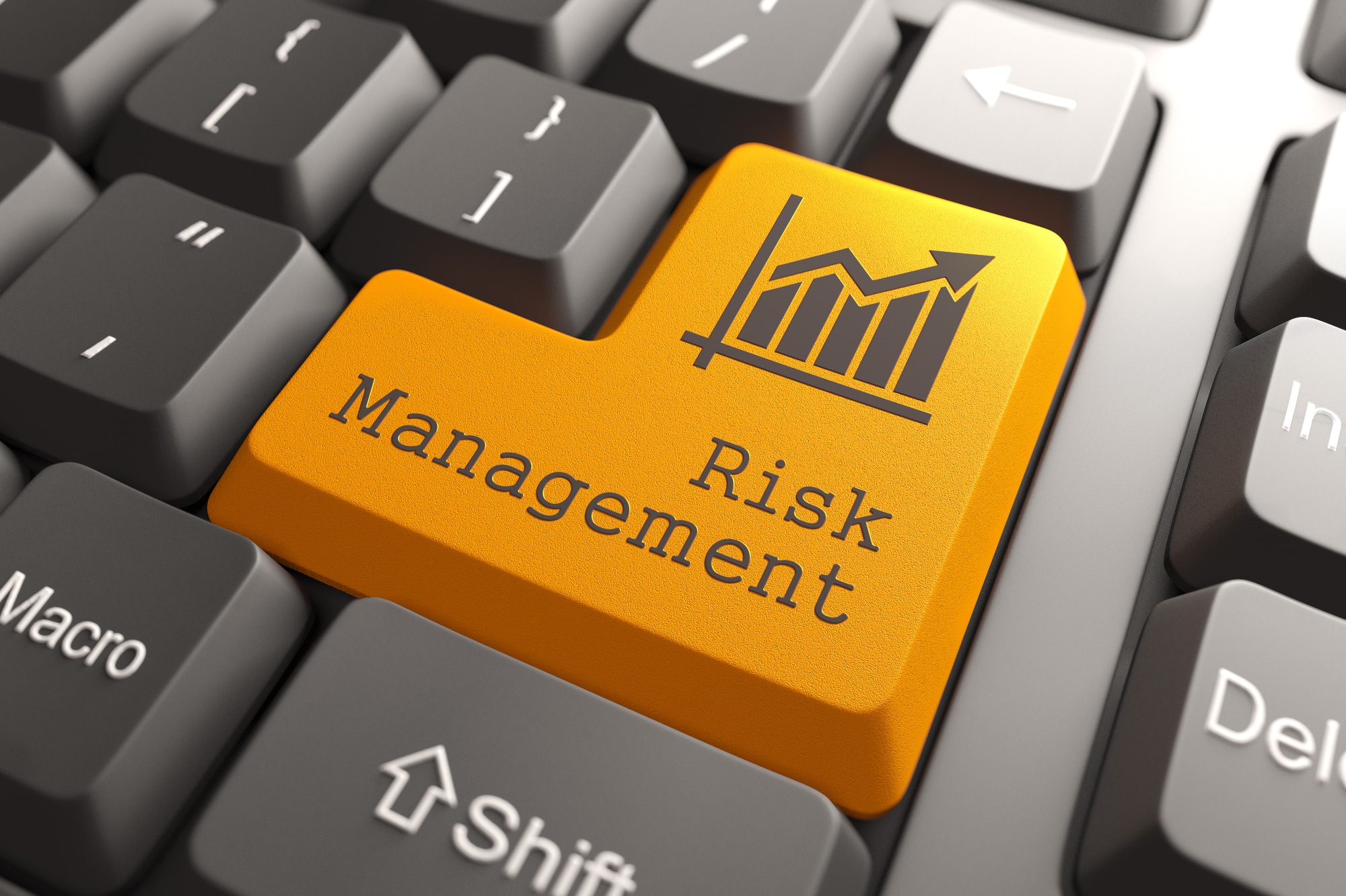
Recovered Resources
The resources recovered from waste management can also be used to create new products and reduce waste. This practice reduces landfill space and conserves natural resources. It can also be used to reduce the raw material requirements for manufacturing processes. Recycling municipal solid waste, construction waste and industrial waste can all be used to make new products. Examples include plastic and glass bottles.
Many sectors are able to benefit from the recovered resources. They can be used to meet increasing demands for scarce natural resources such as topsoil, nutrients, and improve soil conditions. Regulations and competitive pressures are also important drivers of resource recovery. Some states have passed laws mandating the diversion and disposal of organic waste from landfills.
FAQ
What does the term "project management” mean?
It refers to the management of activities related to a project.
We help you define the scope of your project, identify the requirements, prepare the budget, organize the team, plan the work, monitor progress and evaluate the results before closing down the project.
What is the difference in Six Sigma and TQM?
The main difference in these two quality management tools lies in the fact that six sigma is focused on eliminating defects and total quality management (TQM), emphasizes improving processes and reducing costs.
Six Sigma is a methodology for continuous improvement. This approach emphasizes eliminating defects through statistical methods like control charts, Pareto analysis, and p-charts.
This method has the goal to reduce variation of product output. This is achieved by identifying and addressing the root causes of problems.
Total quality management is the measurement and monitoring of all aspects within an organization. This includes training employees to improve their performance.
It is often used to increase productivity.
What kind of people use Six Sigma?
People who have worked with statistics and operations research will usually be familiar with the concepts behind six sigma. However, anyone involved in any aspect of business can benefit from using it.
Because it requires a high degree of commitment, only leaders with strong leadership skills can implement it successfully.
What are the steps in the decision-making process in management?
The decision-making process for managers is complex and multifaceted. It involves many elements, including analysis, strategy. planning. implementation. measurement. evaluation. feedback.
Remember that people are humans just like you, and will make mistakes. This is the key to managing them. As such, there is always room for improvement, especially if you're willing to put forth the effort to improve yourself first.
This video explains the process of decision-making in Management. We discuss the different types of decisions and why they are important, every manager should know how to navigate them. You'll learn about the following topics:
What is Kaizen?
Kaizen refers to a Japanese term that stands for "continuous improvements." It is a philosophy which encourages employees in continuously improving their work environment.
Kaizen is founded on the belief of everyone being able to do their job well.
What is the role of a manager in a company?
There are many roles that a manager can play in different industries.
A manager generally manages the day to-day operations in a company.
He/she will ensure that the company fulfills its financial obligations.
He/she makes sure that employees adhere to the rules and regulations as well as quality standards.
He/she oversees marketing campaigns and plans new products.
What are management concepts?
Management concepts are the principles and practices used by managers to manage people, resources. They cover topics such as job descriptions and performance evaluations, human resource policies, training programs, employee motivation, compens systems, organizational structure, among others.
Statistics
- As of 2020, personal bankers or tellers make an average of $32,620 per year, according to the BLS. (wgu.edu)
- Hire the top business lawyers and save up to 60% on legal fees (upcounsel.com)
- The BLS says that financial services jobs like banking are expected to grow 4% by 2030, about as fast as the national average. (wgu.edu)
- UpCounsel accepts only the top 5 percent of lawyers on its site. (upcounsel.com)
- The profession is expected to grow 7% by 2028, a bit faster than the national average. (wgu.edu)
External Links
How To
How do you apply the Kaizen method to your life?
Kaizen means continuous improvement. The term was coined in the 1950s at Toyota Motor Corporation and refers to the Japanese philosophy emphasizing constant improvement through small incremental changes. It's a team effort to continuously improve processes.
Kaizen is one of the most effective methods used in Lean Manufacturing. In this concept, employees who are responsible for the production line must identify problems that exist during the manufacturing process and try to solve them before they become big issues. This will increase the quality and decrease the cost of the products.
Kaizen is about making everyone aware of the world around them. It is important to correct any problems immediately if they are discovered. If someone spots a problem while at work, they should immediately report it to their manager.
Kaizen follows a set of principles. Always start with the end product in mind and work our way back to the beginning. To improve our factory, for example, we need to fix the machines that produce the final product. We then fix the machines producing components, and the machines producing raw materials. Then we fix the workers, who directly work with these machines.
This approach is called 'kaizen' because it focuses on improving everything steps by step. Once the factory is fixed, we return to the original site and work our way back until we get there.
To implement kaizen in your business, you need to find out how to measure its effectiveness. There are several ways to determine whether kaizen is working well. Another method is to see how many defects are found on the products. Another method is to determine how much productivity has improved since the implementation of kaizen.
A good way to determine whether kaizen has been implemented is to ask why. You were trying to save money or obey the law? Did you really think that it would help you achieve success?
Let's say you answered yes or all of these questions. Congratulations! Now you're ready for kaizen.