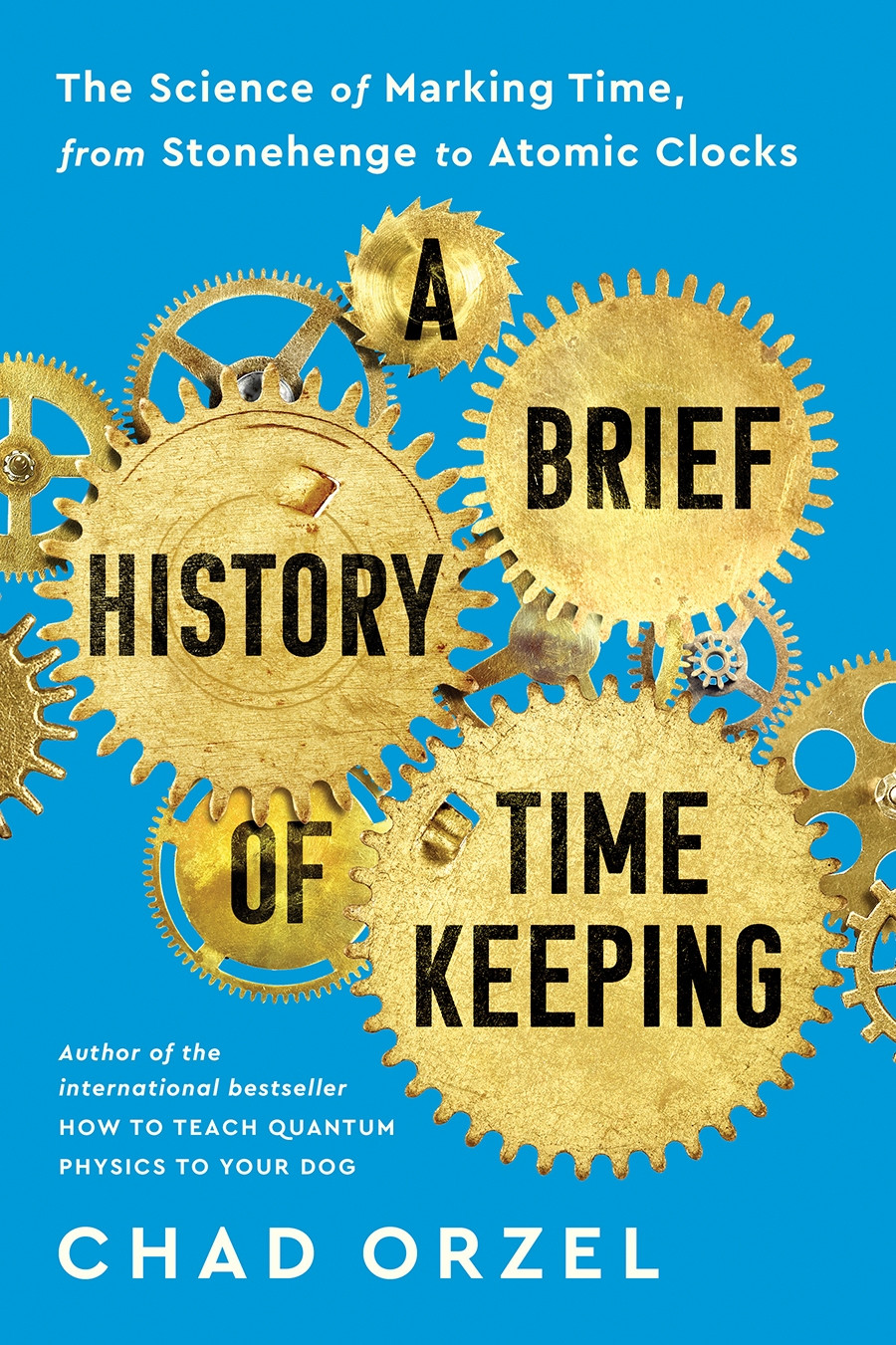
The Project Management Body of Knowledge (PMBOK) was first published in electronic format on March 27, 1987. It contains nine knowledge area and 37 processes. The PMBOK Guide 2000 Edition is 211 pages long and includes nine knowledge categories and 39 processes. The fourth edition, which contains 467 pages with 47 processes, is the fourth PMBOK Guide. The fifth edition of PMBOK Guide, which was published in December 2012 and includes 619 ITTO, was released in December 2012. The PMBOK Guide provides a complete set of project management methods and practices that help to manage a project.
Closing of projects
The project closure process has several phases. Its goal is to complete all tasks and activities, as well as the planned work. It also involves archiving project information, and releasing resources for the organizational team. PMbok's closing processes make it simple to manage this critical phase of project management. These processes are categorized as follows:
A successful project closure ties together all aspects of the project, and the most effective leaders create an inclusive space for everyone. They demonstrate to team members how they contributed to the success of the project. Team members should be involved in the final phase of the project. This helps them understand their roles and ensures that it is meaningful. This phase should provide an opportunity for reflection and self-evaluation. This step is essential to ensure that the project's closure is successful.
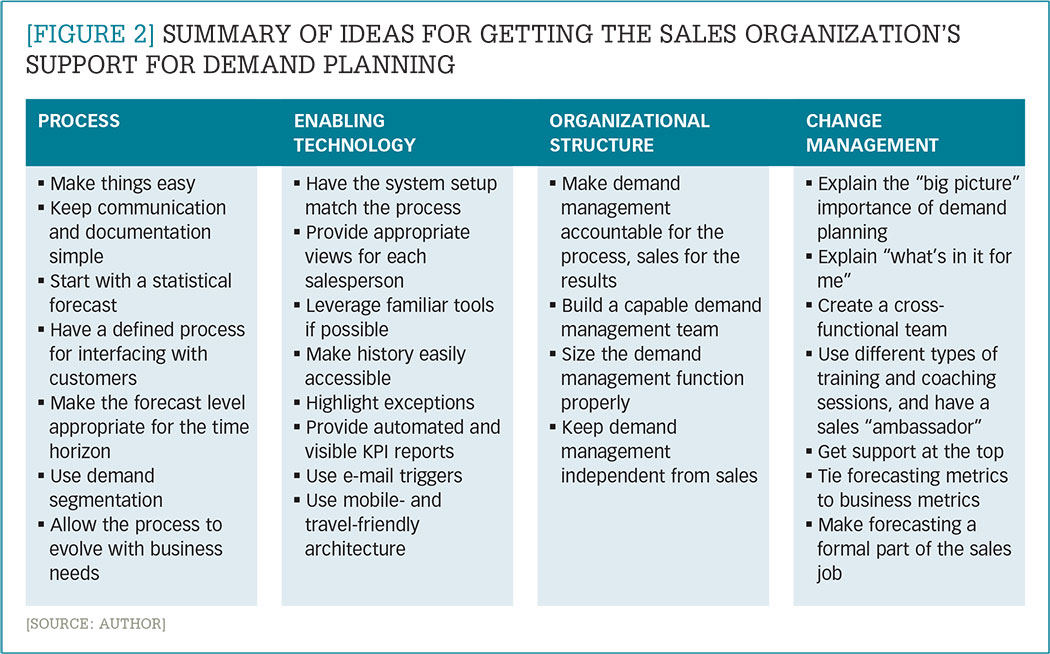
Knowledge areas
The Project Management Body of Knowledge (PMBok) defines three Knowledge Areas. These knowledge areas, regardless of their management quality, will influence the project's success. These knowledge areas need to be considered as separate but interrelated. These areas are critical to the success and sustainability of a project. These Knowledge Areas should be built on best practices for project management. This will allow you to make informed decisions about how to manage these areas.
The Project Management Knowledge Area is comprised of four processes: Identifying risk, performing qualitative or quantitative risk analyses, planning risks responses, and monitoring. These processes help to minimize the effects of risk on a project. Project Procurement Management Knowledge Area includes managing stakeholder engagement and conducting procurement controls. This knowledge section is the latest addition of the PMBOK. You need to upgrade your knowledge base. Consider the new content if you haven’t updated your knowledge to keep up with changing project demands.
Process groups
The PMBOK Guide recognizes five main Process Groups. Each process is interconnected and contributes to project success. These groups are useful for project managers who want to improve their PM skills in order achieve project objectives. The five Process Groups are related by their outputs. Each process gives input to the others. For instance, the Initiating Process Group contributes towards the Planning Process Group. This in turn provides input into the Executing Process Group.
PMBOK has also established knowledge areas, which divide processes according their knowledge requirements. The most common knowledge area is "Project Cost Management," although specific tasks such managing costs can take place in different parts. Each process group has a logical structure. You can find more information on each of these groups at the PMBOK Process Groups webpage. Below is a diagram that shows how each group fits into the overall project.
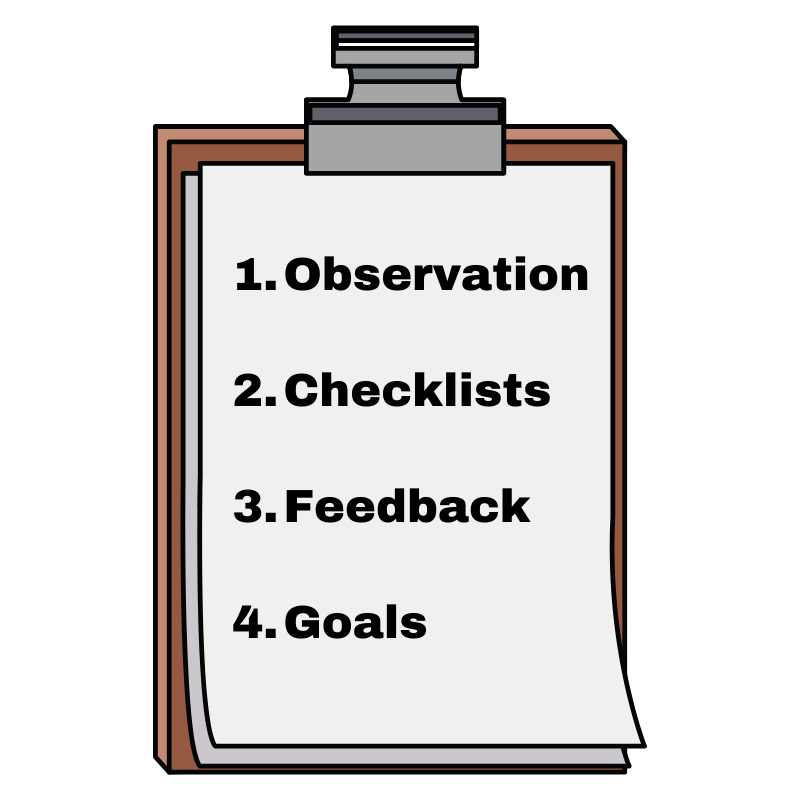
Alternatives to PMBOK
There are many options available if you need a new way to manage your project. While PMBOK is a good foundation, it doesn't have everything you need to run a successful project. You can also use other methods to manage projects such as Enterprise Analysis and requirements management. These alternatives focus more on specific aspects of a given project, such a business need, than a specific type.
PMBOK is a great option if you are interested in using a methodology, but don't have the time to learn it. PMBOK Guide includes best practices, terminology and guidelines to help you manage your projects. It is also an excellent resource for large enterprise projects. The guide helps you define roles and responsibilities, ensures that projects stay on track, endorses the concept of management by exception, and provides guidance. If you are managing a small task, however, it can be cumbersome and time-consuming.
FAQ
How does Six Sigma function?
Six Sigma uses statistical analysis to find problems, measure them, analyze root causes, correct problems, and learn from experience.
First, identify the problem.
The data is then analyzed and collected to identify trends.
Next, corrective steps are taken to fix the problem.
Finally, data will be reanalyzed to determine if there is an issue.
This cycle continues until there is a solution.
How can a manager improve his/her managerial skills?
Good management skills are essential for success.
Managers must continuously monitor the performance levels of their subordinates.
It is important to take immediate action if your subordinate doesn't perform as expected.
You should be able pinpoint what needs to improve and how to fix it.
Why is it so hard to make smart business decisions?
Complex business systems have many moving parts. The people who run them must juggle multiple priorities at once while also dealing with uncertainty and complexity.
Understanding how these factors impact the whole system is key to making informed decisions.
It is important to consider the functions and reasons for each part of the system. Then, you need to think about how these pieces interact with one another.
Ask yourself if there are hidden assumptions that have influenced your behavior. If you don't have any, it may be time to revisit them.
Asking for assistance from someone else is a good idea if you are still having trouble. You may be able to see things from a different perspective than you are and gain insight that can help you find a solution.
How do you effectively manage employees?
Managing employees effectively means ensuring that they are happy and productive.
This includes setting clear expectations for their behavior and tracking their performance.
Managers need clear goals to be able to accomplish this.
They should communicate clearly to staff members. And they need to ensure that they reward good performance and discipline poor performers.
They also need to keep records of their team's activities. These include:
-
What did we accomplish?
-
How much work did you put in?
-
Who did it?
-
It was done!
-
Why did it happen?
This information can be used for monitoring performance and evaluating results.
Statistics
- UpCounsel accepts only the top 5 percent of lawyers on its site. (upcounsel.com)
- The average salary for financial advisors in 2021 is around $60,000 per year, with the top 10% of the profession making more than $111,000 per year. (wgu.edu)
- This field is expected to grow about 7% by 2028, a bit faster than the national average for job growth. (wgu.edu)
- Our program is 100% engineered for your success. (online.uc.edu)
- As of 2020, personal bankers or tellers make an average of $32,620 per year, according to the BLS. (wgu.edu)
External Links
How To
How can you use the Kaizen method?
Kaizen means continuous improvement. The Japanese philosophy emphasizes small, incremental improvements to achieve continuous improvement. This term was created by Toyota Motor Corporation in 1950. It's where people work together in order to improve their processes constantly.
Kaizen is one method that Lean Manufacturing uses to its greatest advantage. Kaizen is a concept where employees in charge of the production line are required to spot problems during the manufacturing process before they become major issues. This is how you can improve the quality and lower the cost.
Kaizen is an approach to making every worker aware and alert to what is happening around them. To prevent problems from happening, any problem should be addressed immediately. If someone spots a problem while at work, they should immediately report it to their manager.
Kaizen is based on a few principles. Always start with the end product in mind and work our way back to the beginning. To improve our factory, for example, we need to fix the machines that produce the final product. Then, we fix the machines that produce components and then the ones that produce raw materials. Then we fix the workers, who directly work with these machines.
This method is known as kaizen because it focuses upon improving every aspect of the process step by step. Once we have finished fixing the factory, we return to the beginning and work until perfection.
How to measure kaizen's effectiveness in your business is essential to implement it. There are many methods to assess if kaizen works well. One of these ways is to check the number of defects found on the finished products. Another way is determining how much productivity increased after implementing kaizen.
You can also find out if kaizen works by asking yourself why you decided to implement it. Was it just because it was the law or because you wanted to save money? It was a way to save money or help you succeed.
Let's say you answered yes or all of these questions. Congratulations! You are now ready to begin kaizen.