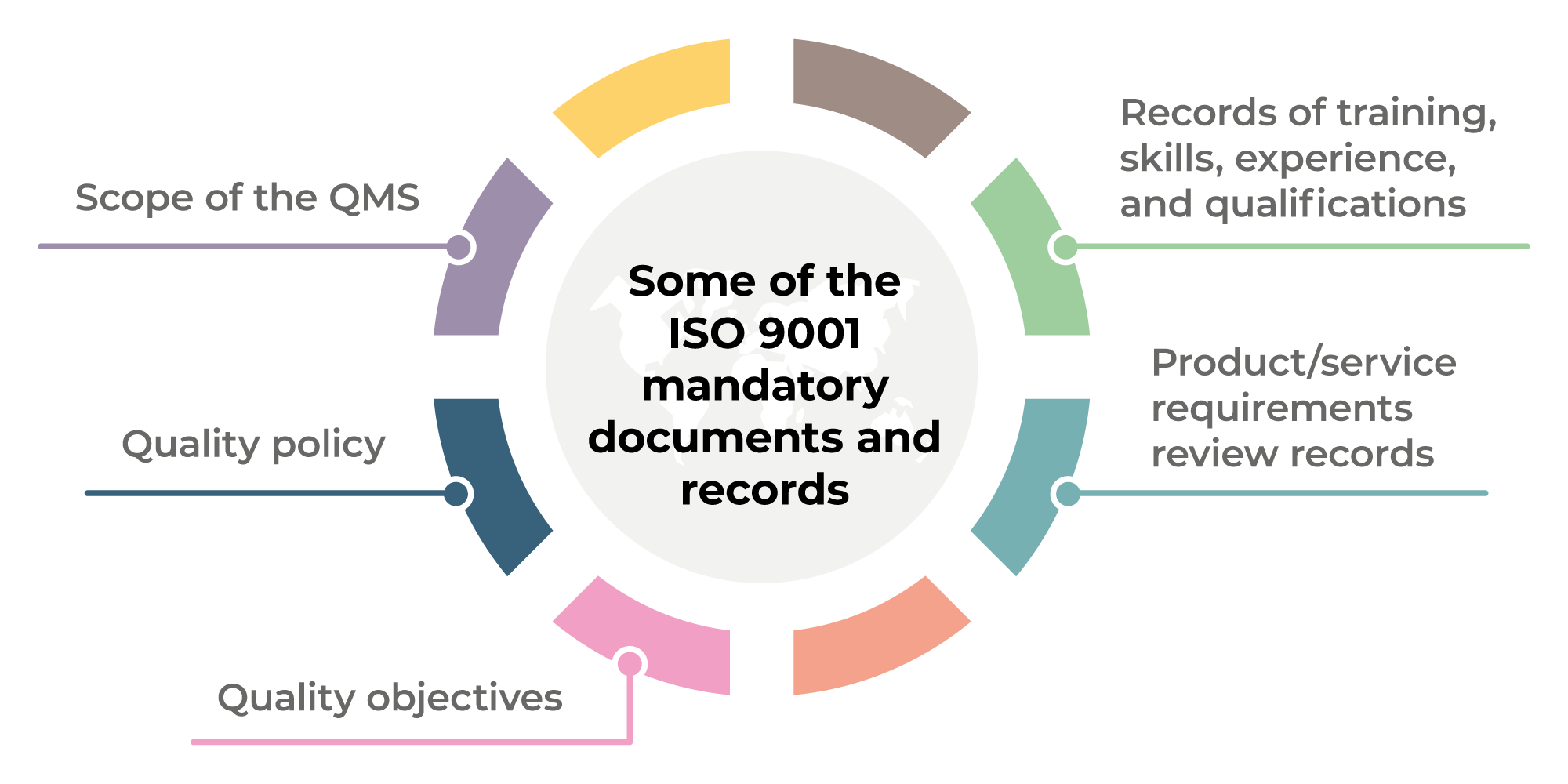
Inventory management involves the purchase, storage, use, packaging, and shipment of goods. This ensures that companies have enough finished goods in stock to meet customer demand. It allows companies to keep track of buyer trends over the years and improves their time to market. It is essential to know how to efficiently use inventory to ensure effective inventory management.
Inventory management is the act of purchasing, storing, using and packaging goods for shipping.
The key to running a business is inventory management. It is essential to running a successful company as it can prevent financial problems. It can be challenging to manage inventory, especially when your business has multiple locations. You might have several warehouses. This means that inventory levels must be monitored at all locations. It can be tedious to manage inventory, but it is critical for your business.
There are many methods for managing inventory. One method is economic order number (EOQ). To determine how much inventory a company should own, this measurement considers the total cost of production as well as consumer demand. Using EOQ can help a business remain profitable and free up cash.
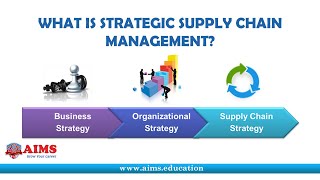
It ensures the availability and quality of finished goods
Companies that are able to manage their inventory effectively can be distinguished from their peers. It includes sorting products and storing them in accordance with demand. This may include cross docking or dropshipping. Software systems can also be used to monitor inventory levels. With the right software system, a business can manage its stock levels so as to maximize inventory planning. Inventory management begins when a customer places an online order or visits a physical storefront.
Another type is inventory management that focuses on raw material. These can either be purchased from another firm or made in house. This inventory includes items in the production process such as nuts, screws and washers. It may also include work, in-process inventory. This includes parts used for the packaging and maintenance of finished goods. Part of the inventory is also basic office supplies, like paper and pencils.
It helps companies keep track of buyer trends over time
Inventory management is the process of tracking the items a company has on hand. It involves the review of data every so often to determine what stock should be ordered and when. This is an important step because it can help companies discover patterns and trends in buyer behavior. You can identify shrinkage problems by keeping track your inventory.
Inventory management also helps companies identify deadstock or obsolete products. These are products that customers have stopped buying or are nearing the deadstock stage. Inefficient warehouse organisation can also cause problems like inadequate signage, unsafe storage conditions, and insufficient walking space. It is also possible to use the inventory turnover rate (ITR), which can be used as a measure of how frequently a company replaces its inventory. The ITR is a measure of how likely a company is to sell its majority of inventory within a given cycle.
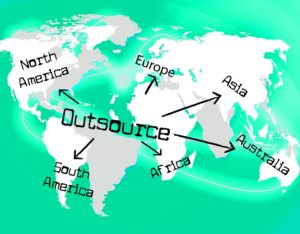
It improves time to market
Inventory management allows companies ship items faster and ensures they have enough stock at all times. Inventory management also helps to reduce the chance of cancelled orders and out-of-stock products. Customers often get frustrated when a product is out of stock, and inventory management can help you avoid this.
No matter the size of your business, managing inventory is essential. It is a complicated task that requires many decisions. Excel formulas may be used by small businesses to track stock and determine reorder points. Enterprise resource planning software is used by larger organizations. SaaS-based applications are also available to large corporations.
FAQ
What are the 3 main management styles?
There are three types of management: participative, laissez faire, and authoritarian. Each style has strengths and flaws. Which style do yo prefer? Why?
Authoritarian - The leader sets the direction and expects everyone to comply with it. This style works well if an organization is large and stable.
Laissez-faire is a leader who allows everyone to make their own decisions. This style works best when an organization is small and dynamic.
Participative - The leader listens to ideas and suggestions from everyone. This style is most effective in smaller organizations, where everyone feels valued.
What is the difference of a program and project?
A project is temporary; a program is permanent.
Projects usually have a goal and a deadline.
It is often done in a team that reports to another.
A program typically has a set goal and objective.
It is usually implemented by a single person.
How does a manager motivate his/her employees?
Motivation is the desire to do well.
Enjoyable activities can motivate you.
You can also get motivated by seeing your contribution to the success or the improvement of the organization.
For example: If you want to be a doctor, you might find it more motivating seeing patients than reading medical books all day.
A different type of motivation comes directly from the inside.
You might feel a strong sense for responsibility and want to help others.
Or you might enjoy working hard.
If you feel unmotivated, ask yourself why.
Next, think of ways you can improve your motivation.
What are management concepts, you ask?
Management concepts are the practices and principles managers use to manage people or resources. They cover topics such as job descriptions and performance evaluations, human resource policies, training programs, employee motivation, compens systems, organizational structure, among others.
What is the difference between Six Sigma Six Sigma and TQM?
The main difference in these two quality management tools lies in the fact that six sigma is focused on eliminating defects and total quality management (TQM), emphasizes improving processes and reducing costs.
Six Sigma stands for continuous improvement. It emphasizes the elimination of defects by using statistical methods such as control charts, p-charts, and Pareto analysis.
This method aims to reduce variation in product production. This is done by identifying and correcting the root causes of problems.
Total quality management refers to the monitoring and measurement of all aspects in an organization. It also includes the training of employees to improve performance.
It is often used as a strategy to increase productivity.
Statistics
- Our program is 100% engineered for your success. (online.uc.edu)
- Hire the top business lawyers and save up to 60% on legal fees (upcounsel.com)
- Your choice in Step 5 may very likely be the same or similar to the alternative you placed at the top of your list at the end of Step 4. (umassd.edu)
- The BLS says that financial services jobs like banking are expected to grow 4% by 2030, about as fast as the national average. (wgu.edu)
- 100% of the courses are offered online, and no campus visits are required — a big time-saver for you. (online.uc.edu)
External Links
How To
How do I get my Six Sigma certification?
Six Sigma can be used to improve quality and efficiency. It is a process that helps businesses achieve consistent results in their operations. The name is derived from the Greek word "sigmas", which means "six". Motorola created this process in 1986. Motorola recognized that they had to standardize their manufacturing processes to produce faster and more affordable products. They had been having problems with consistency because of the many different people who were doing the work. They used statistical tools such as Pareto analysis, control charts, and Pareto analysis to resolve the problem. After this, they would apply these techniques to every part of the operation. After applying the technique, they could make improvements wherever there was potential. To get Six Sigma certified, there are three key steps. Find out if you are qualified. You will need to complete some classes before you can start taking the tests. After passing the classes, you will be able to take the tests. You'll need to go back and review all the information you received in class. You'll then be prepared to take the exam. You will be certified if you pass the test. Finally, your certifications will be added to your resume.