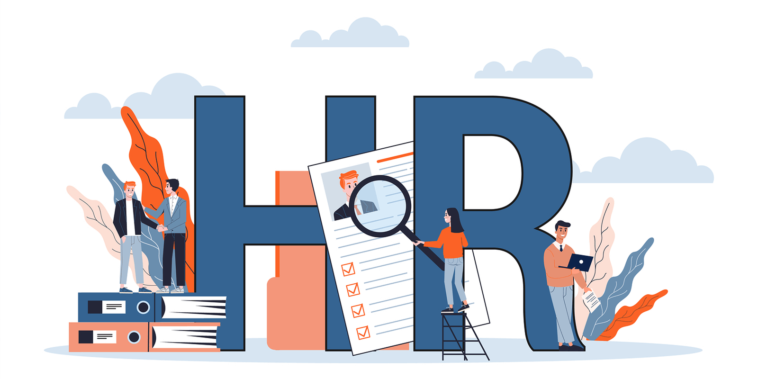
Construction contracts law differs from one country or another. There are common principles, but they can also differ from jurisdiction to jurisdiction. Different countries use different methods to resolve disputes. Get legal advice to ensure the law is applicable to your case. There are many ways to resolve disputes relating to construction contracts.
German construction law
Recent amendments to the German construction law could have consequences for the implementation of standard business terms in construction projects. The FIDIC Silver Book 2017 is based in part on the 1999 edition. However, it has been much debated about whether or not it is compatible to German law which codifies standard terms in section 305 BGB. This law is mandatory and is enforced in state courts.
The construction principal faces many problems if there are material defects during construction. He may choose to continue construction but he must identify and prove the defects. Moreover, any delays can lead to time-barring of the warranty claims. This could lead to financial losses and excessive German construction court proceedings for the principal.
Conditions for claiming damages in the event of delays in construction
It is important to clearly and precisely define the conditions for claiming damages for delays in a construction project. A construction contract will typically list items that could be delayed and the reasons for the delay. Notifying the other party in privity of any delay is important. The contractor should try to allocate the delay between the items.
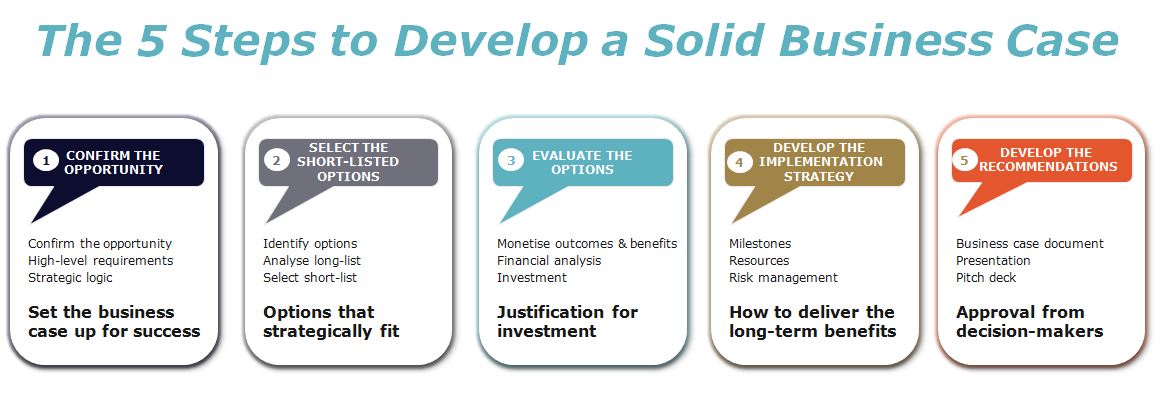
To determine whether a condition was not met, the courts now use a reasonable foreseeability test. An owner might know that a large piece of equipment won't be delivered within a given time frame. To mitigate this risk, the owner may include a clause that allows for a 60-day extension and a reasonable delay. Contractors are not entitled to damages if this clause violates.
Liability for architect
Liability of an architect in construction law arises when a design or plan is defective or fails to meet its requirements. An architect cannot claim that his employer gave permission for him to design unsafe or other defects. In cases such as this, the architect will have to prove that he did not commit a material breach of duty.
It is important to consider several factors when determining an architect's liability. First, the architect should have undertaken all the relevant investigations. If the architect failed to do so, the client could sue him for negligence and seek compensation for the damages incurred.
Subcontractor liability
In a lawsuit involving construction, a subcontractor might be found liable. If the work was not up-to-standard, a subcontractor could be held responsible. This works in the same manner as the contractor-owner negligence doctrine. Subcontractor liability is different. The subcontractor must be aware of the defect or should reasonably have known about it.
Indemnity provisions are a part of construction law. If the other party is deemed responsible, indemnity clauses can reduce a subcontractor’s liability. Many contractors and subcontractors sign indemnity agreement. These agreements are used to ensure that the other party is not liable for any problems that arise during the construction process. Indemnity agreements are also a way to protect both sides by limiting their liability.
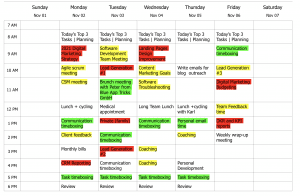
Liability of the owner
The nature of the defect determines the extent of the owner's liability under construction law. Most defects are not the fault of the owner. The contractor is responsible to complete the project in accordance with the plans and specifications. In some instances, however, it may be the owner who is responsible for the defect. The owner could have misrepresented the site to the contractor which can lead to structural failure.
A defective product may also lead to a construction defect. Subcontractors may also file claims against the owner for economic damage if they are unable to perform the job. This can be done through a Uniform Commercial Code claim against the manufacturer.
FAQ
Why is it important for companies to use project management techniques?
Project management techniques can be used to ensure smooth project execution and meeting deadlines.
This is because many businesses depend heavily upon project work to produce products and services.
These projects must be managed efficiently and effectively by companies.
Without effective project management, companies may lose money, time, and reputation.
What are the top management skills?
No matter if they are running a local business or an international one, management skills are vital. These skills include the ability manage people, finances and resources as well as other factors.
Managerial skills are required when setting goals and objectives and planning strategies, leading employees, motivating them, solving problems, creating policies, procedures, or managing change.
There are so many managerial tasks!
How does a manager motivate his/her employees?
Motivation refers to the desire to perform well.
You can get motivated by doing something enjoyable.
You can also be motivated by the idea of making a difference to the success and growth of your organization.
For example, if you want to become a doctor, you'll probably find it more motivating to see patients than to study medicine books all day.
Motivation comes from within.
You may feel strongly that you are responsible to help others.
You may even find it enjoyable to work hard.
Ask yourself why you aren't feeling motivated.
Next, think of ways you can improve your motivation.
What are the steps involved in making a decision in management?
Managers face complex and multifaceted decision-making challenges. This involves many factors including analysis, strategy and planning, implementation, measurement and evaluation, feedback, feedback, and others.
Remember that people are humans just like you, and will make mistakes. This is the key to managing them. As such, there is always room for improvement, especially if you're willing to put forth the effort to improve yourself first.
In this video, we explain what the decision-making process looks like in Management. We discuss the different types of decisions and why they are important, every manager should know how to navigate them. These topics are covered in this course:
Statistics
- The average salary for financial advisors in 2021 is around $60,000 per year, with the top 10% of the profession making more than $111,000 per year. (wgu.edu)
- The BLS says that financial services jobs like banking are expected to grow 4% by 2030, about as fast as the national average. (wgu.edu)
- As of 2020, personal bankers or tellers make an average of $32,620 per year, according to the BLS. (wgu.edu)
- Your choice in Step 5 may very likely be the same or similar to the alternative you placed at the top of your list at the end of Step 4. (umassd.edu)
- Our program is 100% engineered for your success. (online.uc.edu)
External Links
How To
What is Lean Manufacturing?
Lean Manufacturing processes are used to reduce waste and improve efficiency through structured methods. These processes were created by Toyota Motor Corporation, Japan in the 1980s. The aim was to produce better quality products at lower costs. Lean manufacturing emphasizes removing unnecessary steps from the production process. It consists of five basic elements: pull systems, continuous improvement, just-in-time, kaizen (continuous change), and 5S. Pull systems involve producing only what the customer wants without any extra work. Continuous improvement refers to continuously improving existing processes. Just-in-time refers to when components and materials are delivered directly to the point where they are needed. Kaizen is continuous improvement. This can be achieved by making small, incremental changes every day. The 5S acronym stands for sort in order, shine standardize and maintain. These five elements are combined to give you the best possible results.
Lean Production System
Six key concepts make up the lean manufacturing system.
-
Flow - focuses on moving information and materials as close to customers as possible.
-
Value stream mapping - Break down each stage in a process into distinct tasks and create an overview of the whole process.
-
Five S's, Sort, Set in Order, Shine. Standardize. and Sustain.
-
Kanban - visual cues such as stickers or colored tape can be used to track inventory.
-
Theory of Constraints - Identify bottlenecks in the process, and eliminate them using lean tools such kanban boards.
-
Just-in-time - deliver components and materials directly to the point of use;
-
Continuous improvement is making incremental improvements to your process, rather than trying to overhaul it all at once.