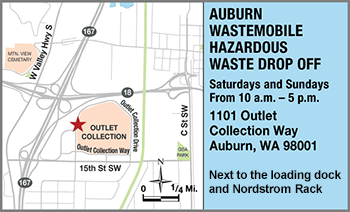
Although it is not required to be a construction manager, it can show your knowledge. After passing a technical examination, and having relevant experience, you can obtain the Certified Construction Management designation. This designation is also expensive. A self-study course is required for applicants on the professional construction manager role, risk allocation and legal issues. After passing the Associate Contractor exam and meeting all other requirements, you will be eligible to earn your certification.
Certification
There are many certifications available for construction managers. The Associate Constructor (AC) certification is the first level, and it demonstrates a high level of construction management skill. ACs are also required to adhere to the Code of Ethics of the AIC, and are ideal for individuals with a background in another industry. This certification must be renewed every three years. The certifications can also be obtained through exams or online.
A certificate in Construction Management can improve a contractor's skills and help them earn more. Employers will be impressed by your construction management certificate. It shows that you have all the skills and experience required to manage a construction job. A certificate in construction management distinguishes small contractors from bigger ones. It shows that you can manage a job. The cost of obtaining a certificate and the type of training required to obtain it vary. The Post-baccalaureate Certificate in Construction Management is for those who have completed a degree in construction. It can help you move up the ladder as a construction manager.
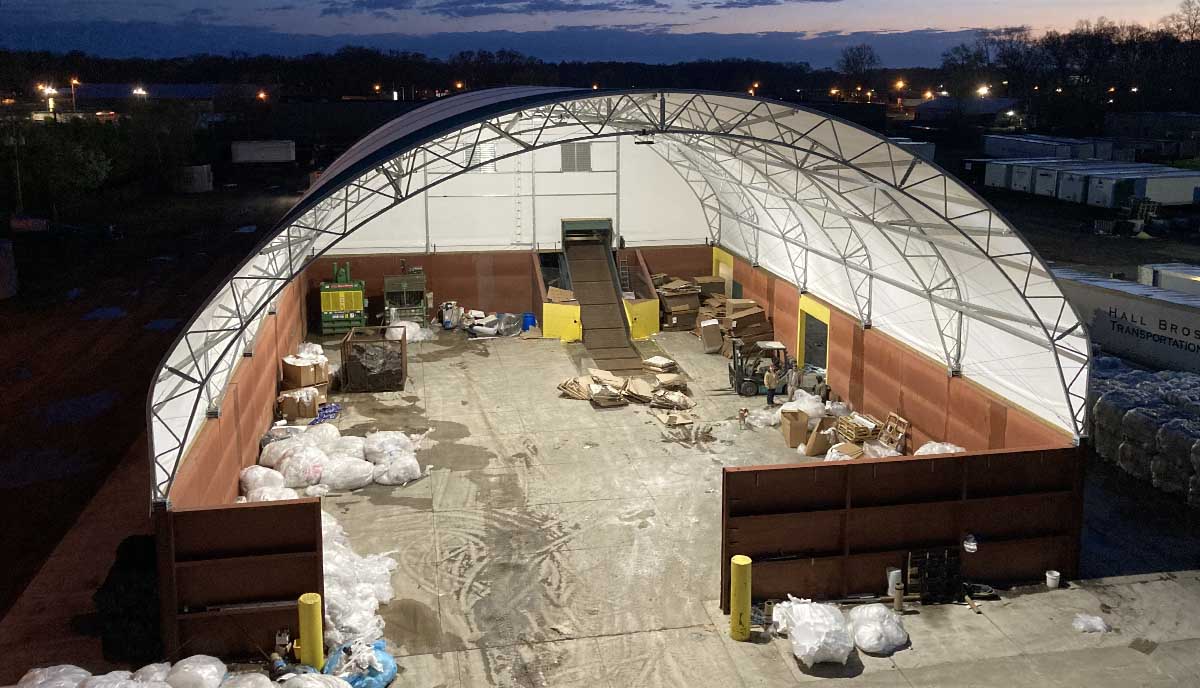
Education
Consider pursuing a certificate, or degree, if your goal is to improve your knowledge in the field. The certification is not required for employment, but it does act as a mark of distinction. It is a proof of your knowledge and dedication in the field. It also offers networking opportunities as the examining body will require proof of supervision hours before you can be awarded the certificate. Professional societies also sponsor credentialing, which can help you advance your career.
The program will provide students with the knowledge and skills necessary to manage projects effectively. Students will acquire knowledge about the project cycle including design-build and general contracting. It emphasizes the value of combining classroom learning and real-world experience. Students will learn how construction projects are evaluated and managed by the various management stages.
Experience
To be a successful career in construction, you need to know the requirements for becoming certified as a construction manager. Although you may have a high school degree, you can start with an internship. While internships are often unpaid, they offer valuable experience in construction. Internships also give students the opportunity to be assistants to licensed construction managers. This can help them understand the responsibilities of their job.
The Certified Construction Manager credential (CCM), is the highest standard in personnel credentials within the Construction Management industry. CCM certification has been accredited only by ANSI. Leading owners-consumers are increasing the use of Certified Construction Managers in construction RFPs. Additionally, a growing number of organizations are supporting the CCM designation by providing financial and technical support.
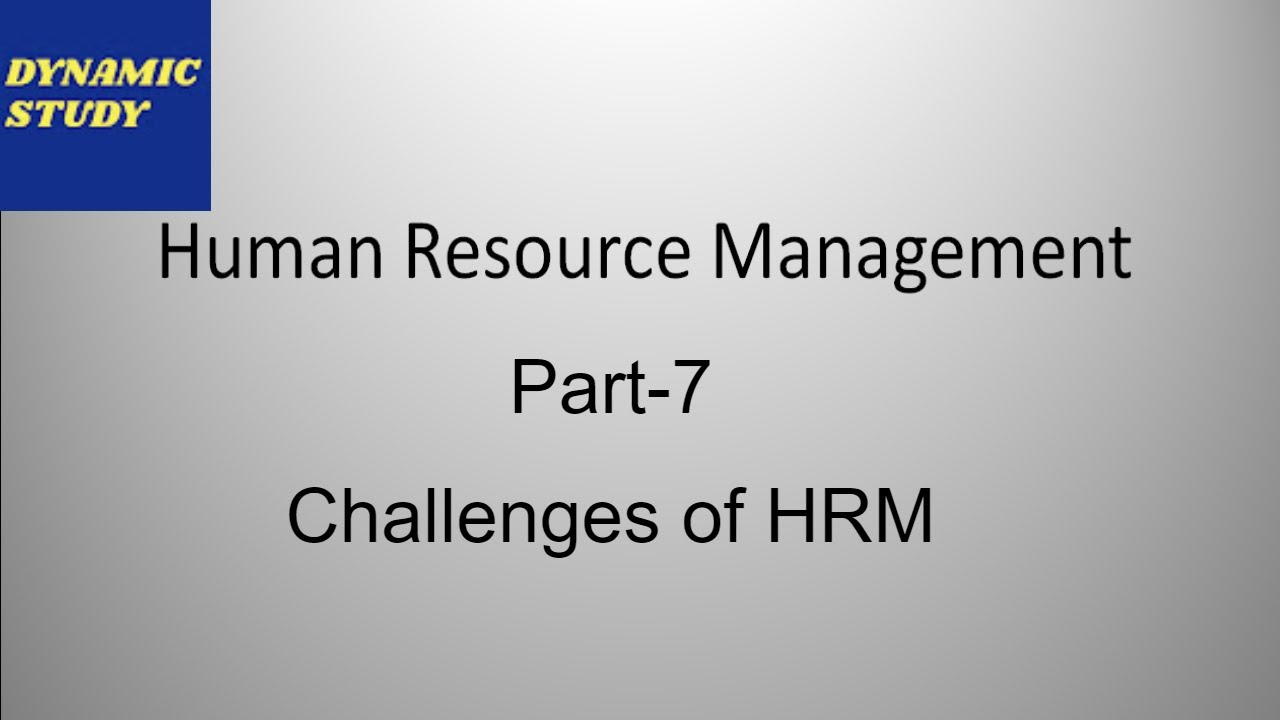
Salary
The salary of a certified construction manager may vary. There are different hazard levels depending on where you work. Management of a high-risk job can result in a higher starting salary and hazard compensation. A higher starting salary could be offered to managers who have been certified workers. This article will show you how to get maximum value from your education. The salary for a certified construction manager ranges from $75,000 to more than $160,000 per annum.
A construction manager makes a significantly higher salary than the average. A construction manager works with many different consultants, including civil engineers and architects, and a number of tradespeople. Certain construction projects will require the expertise of specialists in structural steel and landscaping, painting, excavation sites, and paving roads. They interact with lawyers, local government officials, and other professionals. A construction manager could also consult with city officials or city planners.
FAQ
What is Kaizen?
Kaizen is a Japanese term meaning "continuous improvement." It is a philosophy that encourages employees to constantly look for ways to improve their work environment.
Kaizen is built on the belief that everyone should be able do their jobs well.
How does Six Sigma work
Six Sigma uses statistics to measure problems, find root causes, fix them, and learn from past mistakes.
The first step in solving a problem is to identify it.
Next, data are collected and analyzed in order to identify patterns and trends.
Then corrective actions are taken to solve the problem.
The data are then reanalyzed to see if the problem is solved.
This cycle continues until there is a solution.
What are the steps in the decision-making process in management?
Managers are faced with complex and multifaceted decisions. It involves many elements, including analysis, strategy. planning. implementation. measurement. evaluation. feedback.
It is important to remember that people are human beings, just like you. They make mistakes. As such, there are always opportunities for improvement, especially when you put in the effort to improve yourself.
This video shows you how management makes decisions. We will discuss the various types of decisions, and why they are so important. Every manager should be able to make them. Here are some topics you'll be learning about:
What is the role of a manager in a company?
Each industry has a different role for a manager.
Managers generally oversee the day-today operations of a business.
He/she will ensure that the company fulfills its financial obligations.
He/she will ensure that employees follow all rules and regulations, and adhere to quality standards.
He/she oversees marketing campaigns and plans new products.
Statistics
- Hire the top business lawyers and save up to 60% on legal fees (upcounsel.com)
- Our program is 100% engineered for your success. (online.uc.edu)
- The BLS says that financial services jobs like banking are expected to grow 4% by 2030, about as fast as the national average. (wgu.edu)
- This field is expected to grow about 7% by 2028, a bit faster than the national average for job growth. (wgu.edu)
- As of 2020, personal bankers or tellers make an average of $32,620 per year, according to the BLS. (wgu.edu)
External Links
How To
How do I do the Kaizen Method?
Kaizen means continuous improvement. The term was coined in the 1950s at Toyota Motor Corporation and refers to the Japanese philosophy emphasizing constant improvement through small incremental changes. It's a team effort to continuously improve processes.
Kaizen is one method that Lean Manufacturing uses to its greatest advantage. This concept requires employees to identify and solve problems during manufacturing before they become major issues. This way, the quality of products increases, and the cost decreases.
The main idea behind kaizen is to make every worker aware of what happens around him/her. If something is wrong, it should be corrected immediately so that no problem occurs. If someone spots a problem while at work, they should immediately report it to their manager.
There are some basic principles that we follow when doing kaizen. Always start with the end product in mind and work our way back to the beginning. We can improve the factory by first fixing the machines that make it. We then fix the machines producing components, and the machines producing raw materials. And finally, we fix the workers who work directly with those machines.
This is known as "kaizen", because it emphasizes improving each step. After we're done with the factory, it's time to go back and fix the problem.
How to measure kaizen's effectiveness in your business is essential to implement it. There are many methods to assess if kaizen works well. Another method is to see how many defects are found on the products. Another method is to determine how much productivity has improved since the implementation of kaizen.
You can also find out if kaizen works by asking yourself why you decided to implement it. It was because of the law, or simply because you wanted to save some money. You really believed it would make you successful?
Congratulations if you answered "yes" to any of the questions. You're now ready to get started with kaizen.