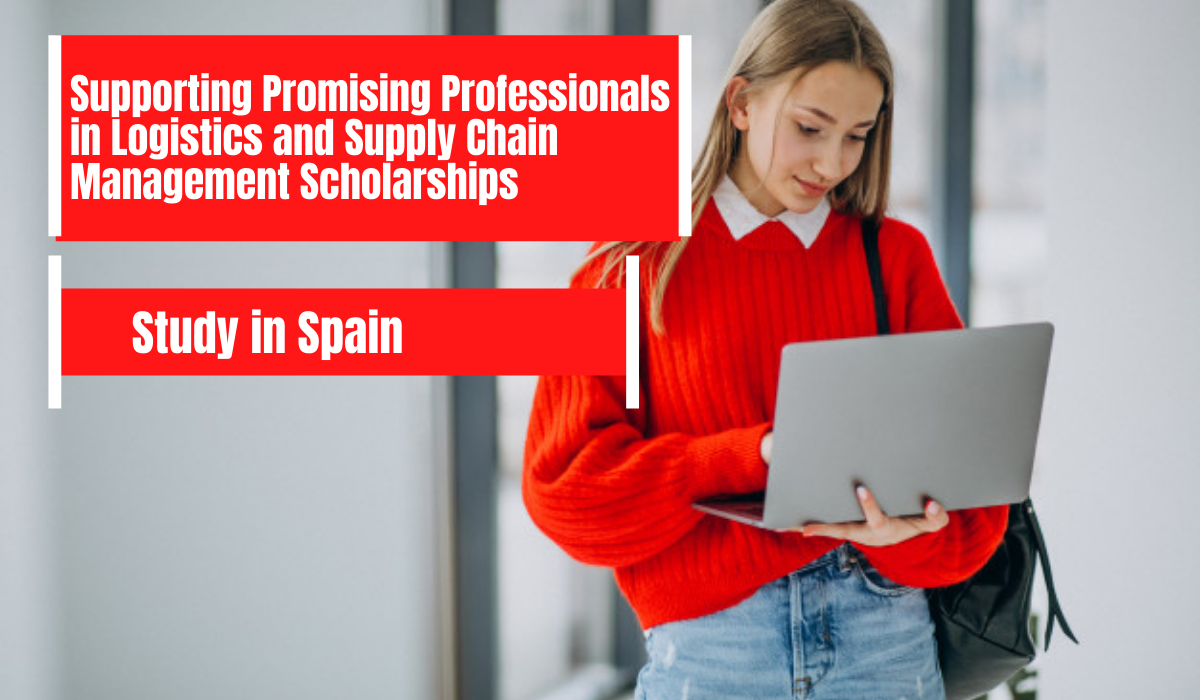
The demand management supply chain is essential for companies that need to meet ongoing customer needs. It is essential to understand how demand works and devise a strategy to address them. Forecasting and Adaptability are important aspects of demand management. This will ensure that customers are satisfied and profits are maximized.
Factors that influence demand in the demand management supply chains
Demand management is critical to your business, no matter if you're a service provider or a product manufacturer. This strategy will allow you to optimize your supply chain and maximize profitability. Demand management can increase your competitive advantage and organizational agility, increase your product availability, and improve your response time to changes in demand. It can also be used to help you quickly and efficiently introduce new products.
Understanding how to balance supply and demand is the key to effective demand management. Properly managing demand will allow you to plan inventory more efficiently, decrease costs, and improve customer service. You can also improve forecasting and avoid excesses. Demand management's ultimate goal is to increase sales and profits.
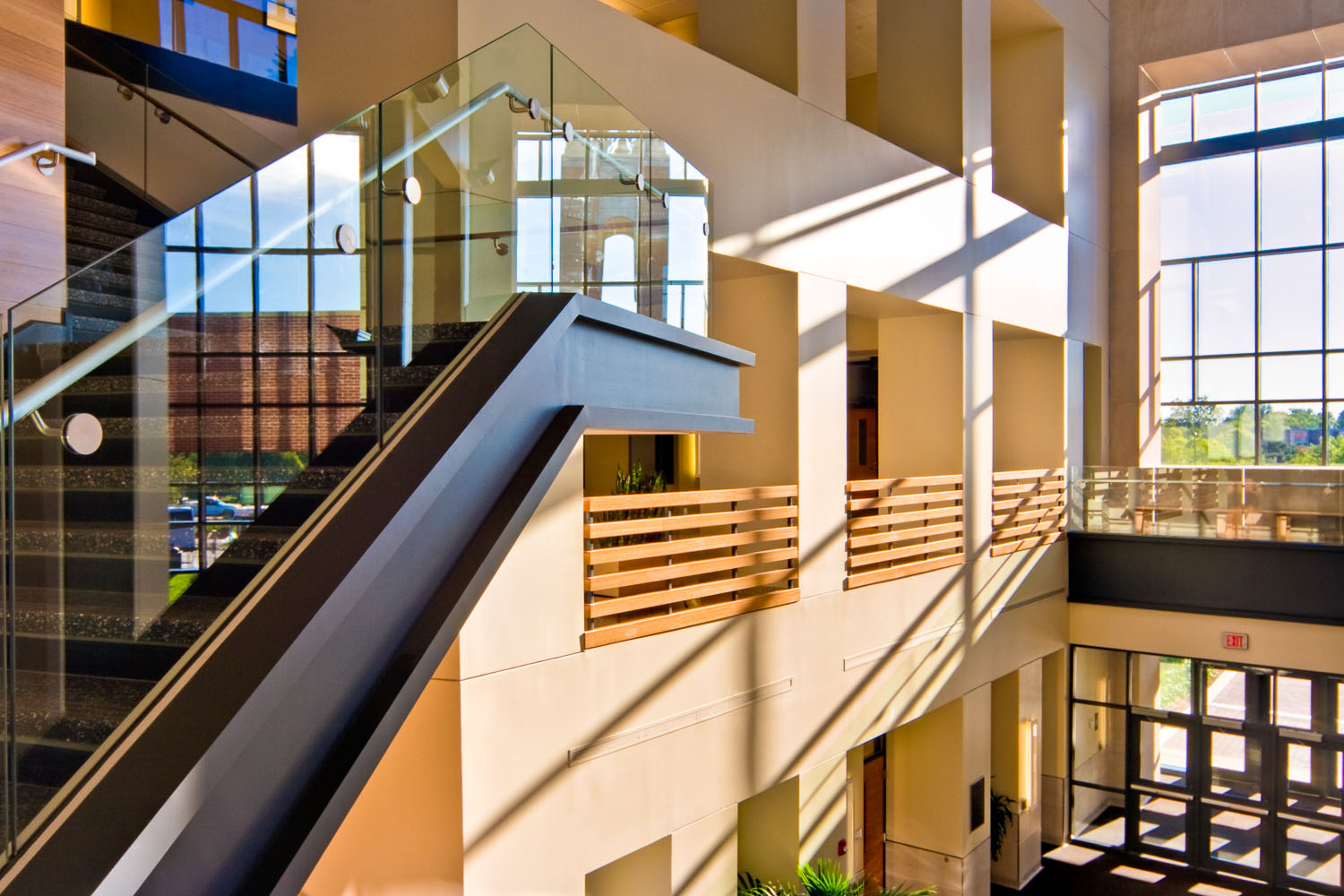
POS data is a crucial data source
POS data is a valuable data source to improve supply chain management and customer demand management. It contains information about customer stock levels, order variability as well sell-through and fill rates. This information allows businesses to make informed decisions. In addition, it enables better communication among various levels.
Software that generates detailed forecasts can be used to create demand planning software. Data can be broken down by SKUs, locations and dates. It is very useful for detecting stockouts, localized sales trends, and detecting stockouts. Working with POS data can prove difficult for new users. Different retail partners may offer the data in different formats. They may also use different data transfer protocols. Moreover, some partners may not be able to share their POS data.
Forecasting is an important part of the demand management supply chain
Forecasting is an important part of demand management supply chain planning. Accurate forecasts help companies determine the level of inventory needed to meet customer demands. They also improve distribution planning and logistics. Companies can avoid stock-outs and the "Bullwhip Effect" by anticipating demand and understanding its impact.
Forecasts are often based on mathematical or computer software. They are updated frequently and should account for all the various intermediates, finished goods, and raw materials involved in a supply chain. Forecasts must also account for independent and dependent demand.
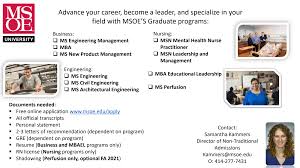
Supply chain management is all about adaptability.
In an increasingly networked business environment, companies need to be flexible and adaptable to changes in customer needs and supply chain conditions. A flexible supply chain architecture can make supply chains more resilient to change and improve competitive advantage. It must be able to consider all aspects and not just those of the end customer in order to be effective.
Companies that are flexible create flexible organizational structures, decentralize decision-making and have adaptability. This allows for greater trust and flexibility among participants. Toyota's automotive supply pyramids are an example of adaptive systems. EBay, which relies on online payment systems and seller ratings, is another example.
FAQ
What is Six Sigma?
This is a method of quality improvement that emphasizes customer service, continuous learning, and customer service. The goal is to eliminate defects by using statistical techniques.
Motorola invented Six Sigma in 1986 as part its efforts to improve manufacturing.
It was quickly adopted by the industry and many companies are now using six-sigma to improve product design, production, delivery, customer service, and product design.
What are the steps that management takes to reach a decision?
Managers are faced with complex and multifaceted decisions. This involves many factors including analysis, strategy and planning, implementation, measurement and evaluation, feedback, feedback, and others.
Management of people requires that you remember that they are just as human as you are, and can make mistakes. You can always improve your performance, provided you are willing to make the effort.
This video shows you how management makes decisions. We discuss different types of decisions as well as why they are important and how managers can navigate them. The following topics will be covered:
How does Six Sigma work
Six Sigma uses statistical analysis for problems to be found, measured, analyzed root causes, corrected, and learned from.
The first step is identifying the problem.
Next, data will be collected and analyzed to determine trends and patterns.
Then corrective actions are taken to solve the problem.
Final analysis of data is done to determine if the problem has been solved.
This continues until you solve the problem.
What are the five management process?
These five stages are: planning, execution monitoring, review and evaluation.
Setting goals for the future is part of planning. It involves setting goals and making plans.
Execution occurs when you actually carry out the plans. You need to make sure they're followed by everyone involved.
Monitoring is a way to track progress towards your objectives. Regular reviews of performance against budgets and targets should be part of this process.
At the end of every year, reviews take place. They allow for an assessment of whether all went well throughout the year. If not, then it may be possible to make adjustments in order to improve performance next time.
After the annual review is complete, evaluations are conducted. It helps identify what worked well and what didn't. It also gives feedback on how well people did.
What's the difference between a program and a project?
A project is temporary, while a program lasts forever.
A project typically has a defined goal and deadline.
It is often done in a team that reports to another.
A program will usually have a set number of goals and objectives.
It is typically done by one person.
Statistics
- Our program is 100% engineered for your success. (online.uc.edu)
- UpCounsel accepts only the top 5 percent of lawyers on its site. (upcounsel.com)
- As of 2020, personal bankers or tellers make an average of $32,620 per year, according to the BLS. (wgu.edu)
- This field is expected to grow about 7% by 2028, a bit faster than the national average for job growth. (wgu.edu)
- The average salary for financial advisors in 2021 is around $60,000 per year, with the top 10% of the profession making more than $111,000 per year. (wgu.edu)
External Links
How To
How can Lean Manufacturing be done?
Lean Manufacturing techniques are used to reduce waste while increasing efficiency by using structured methods. They were developed by Toyota Motor Corporation in Japan during the 1980s. It was designed to produce high-quality products at lower prices while maintaining their quality. Lean manufacturing focuses on eliminating unnecessary steps and activities from the production process. It is composed of five fundamental elements: continuous improvement; pull systems, continuous improvements, just-in–time, kaizen, continuous change, and 5S. Pull systems are able to produce exactly what the customer requires without extra work. Continuous improvement is the continuous improvement of existing processes. Just-in–time refers when components or materials are delivered immediately to their intended destination. Kaizen means continuous improvement. Kaizen involves making small changes and improving continuously. The 5S acronym stands for sort in order, shine standardize and maintain. These five elements are combined to give you the best possible results.
Lean Production System
The lean production system is based on six key concepts:
-
Flow - focus on moving material and information as close to customers as possible;
-
Value stream mapping is the ability to divide a process into smaller tasks, and then create a flowchart that shows the entire process.
-
Five S's: Sort, Shine Standardize, Sustain, Set In Order, Shine and Shine
-
Kanban – visual signals like colored tape, stickers or other visual cues are used to keep track inventory.
-
Theory of constraints - identify bottlenecks in the process and eliminate them using lean tools like kanban boards;
-
Just-in time - Get components and materials delivered right at the point of usage;
-
Continuous improvement is making incremental improvements to your process, rather than trying to overhaul it all at once.