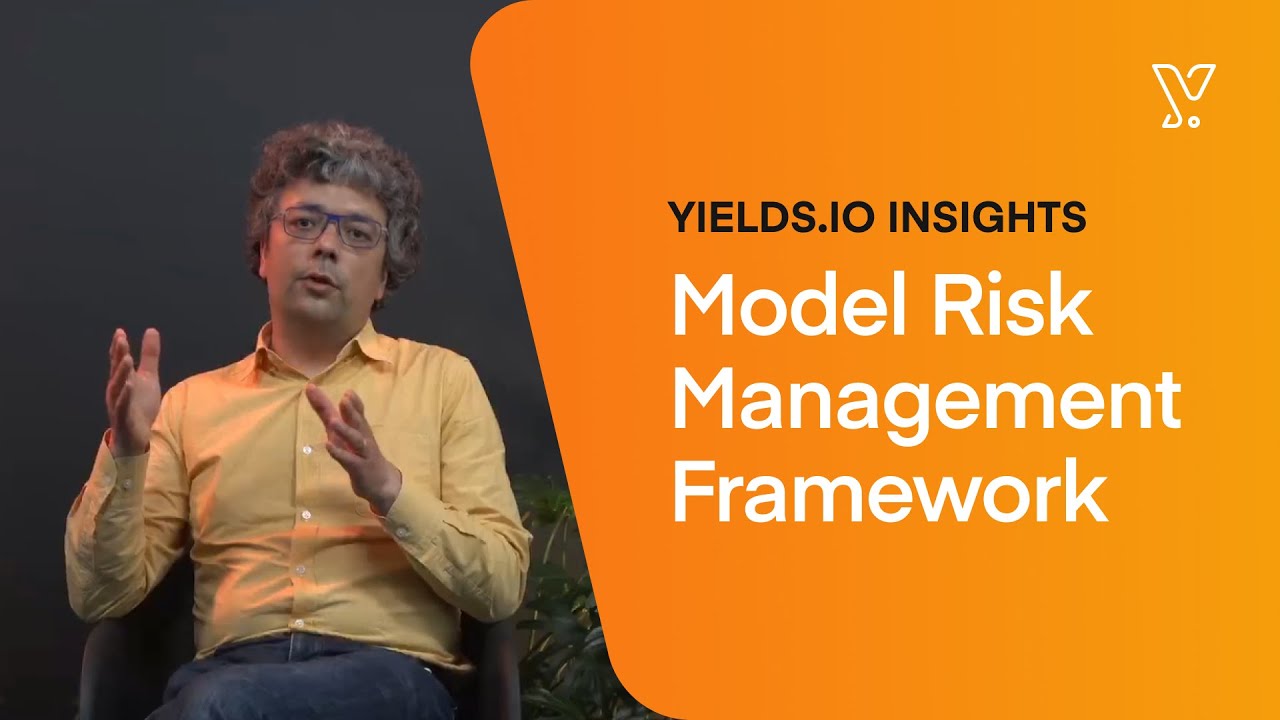
A company must adhere to 14 elements in order to be considered a PSM Program. These elements are Process hazard analysis, Permissible exposure limits and Physical data. These elements are essential for the success of a PSM plan. These elements will ensure that your PSM program is compliant. These elements and their application to your company are covered in the sections below.
Process Hazard Analysis
A process hazard analysis is a critical element of a safety management program. It helps identify potential hazards and evaluate the consequences of failure. This analysis must be done with a group of people who are familiar with the process. It will review the site and include past incidents as well as human factors. The analysis must be reviewed every five years after it is completed. Hazard analysis must be used as part of safety management systems.
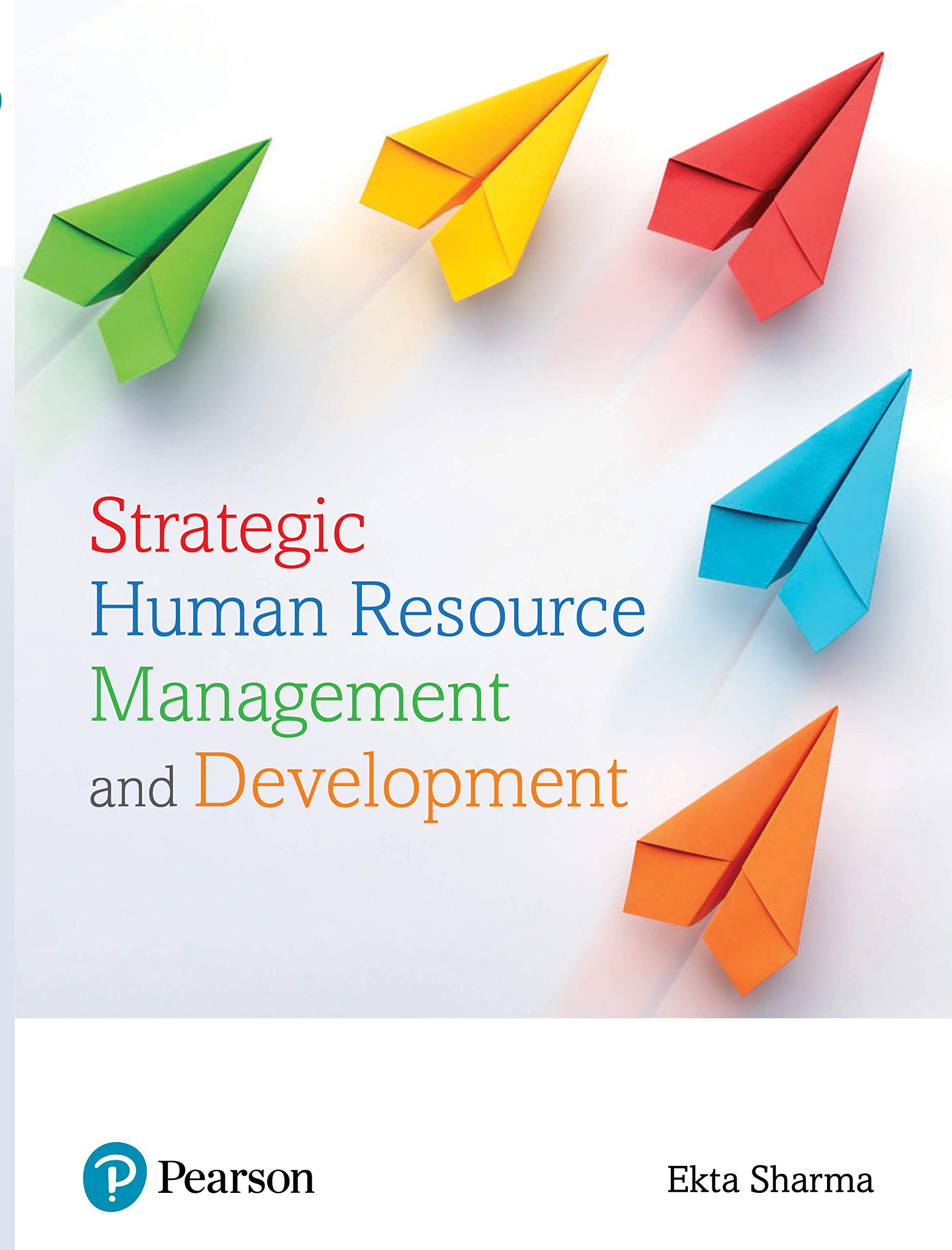
Permissible exposure limits
OSHA Process Safety Management Standard is a set standards that govern processes that involve hazardous chemicals, gases, or fluids. The standard applies to businesses that produce or process hazardous chemicals. It does not apply hydrocarbon fuels only used for the workplace, retail or oil and gaz well drilling. The same applies to unoccupied or remote facilities.
Physical data
PSM is the process of analyzing and controlling the risk of hazardous materials and products. This involves knowing how to safely transport, store, and handle hazardous substances. This can reduce product waste and prevent workplace accidents. It makes it easier to make decisions and allows organizations to prioritize safety and health. PSM is essential for a safe workplace. PSM can also help organizations prevent health emergencies and lower costs.
Data on corrosivity
The PSM standard sets out requirements for how chemicals and other substances should be stored and handled. The PSM also includes requirements for emergency action plans and permit systems, and requires periodic compliance audits. PSM-compliant work environments will prevent injuries and damage, regardless of whether hazardous substances were used in the production processes.
Thermal stability data
OSHA has established a standard for the collection and reporting of PSM thermal stability data. The program will ensure that researchers are aware of possible hazards and minimize the effects of accidental release. It will be updated regularly to reflect new research tasks. It will be made available to all employees. The PSM includes information on toxicity (reactivity), corrosivity and physical properties.
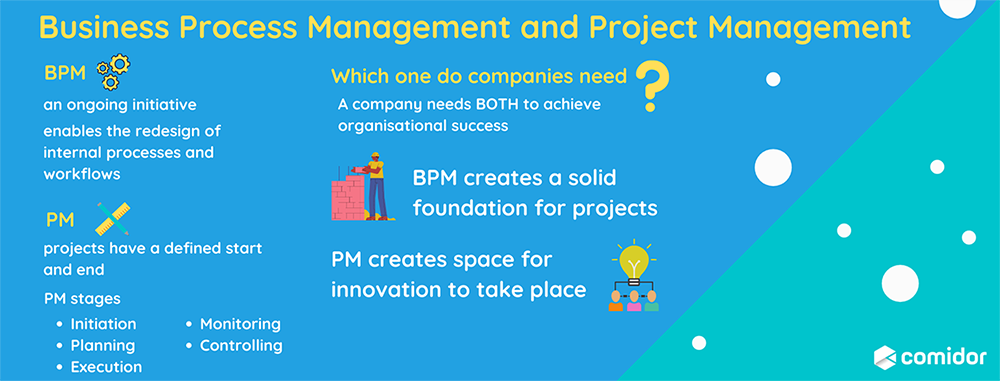
Participation clause
Process Safety Management (PSM), a systematic approach to the prevention and control of hazardous chemicals (HHC)-related process accidents, is an analytical approach. It is a crucial step in improving safety at work and must be applied at all levels of the plant. It contains 14 components that should be implemented. These include employee participation clauses. Listed below are a few examples of these elements and their requirements.
FAQ
What is the difference between leadership and management?
Leadership is about inspiring others. Management is about controlling others.
A leader inspires others while a manager directs them.
A leader motivates people and keeps them on task.
A leader develops people; a manager manages people.
How can we create a successful company culture?
Successful company culture is one where people feel valued and respected.
It is founded on three basic principles:
-
Everyone has something valuable to contribute
-
People are treated fairly
-
Individuals and groups can have mutual respect
These values reflect in how people behave. They will treat others with consideration and courtesy.
They will be respectful of the opinions of other people.
And they will encourage others to share ideas and feelings.
In addition, the company culture encourages open communication and collaboration.
People can freely express their opinions without fear or reprisal.
They know that they will not be judged if they make mistakes, as long as the matter is dealt with honestly.
Finally, the company culture encourages honesty as well as integrity.
Everyone knows that they must always tell truth.
Everyone understands there are rules that they must follow.
Nobody expects to be treated differently or given favors.
What role can a manager fill in a company’s management?
Managers' roles vary from industry to industry.
A manager generally manages the day to-day operations in a company.
He/she is responsible for ensuring that the company meets all its financial obligations and produces the goods or services customers want.
He/she will ensure that employees follow all rules and regulations, and adhere to quality standards.
He/she oversees marketing campaigns and plans new products.
How can a manager improve his/her managerial skills?
It is important to have good management skills.
Managers need to monitor their subordinates' performance.
It is important to take immediate action if your subordinate doesn't perform as expected.
You should be able pinpoint what needs to improve and how to fix it.
Why is project management important for companies?
Project management techniques can be used to ensure smooth project execution and meeting deadlines.
This is because most businesses rely on project work for their products and services.
Companies must manage these projects effectively and efficiently.
Without effective project management, companies may lose money, time, and reputation.
Statistics
- This field is expected to grow about 7% by 2028, a bit faster than the national average for job growth. (wgu.edu)
- Your choice in Step 5 may very likely be the same or similar to the alternative you placed at the top of your list at the end of Step 4. (umassd.edu)
- Hire the top business lawyers and save up to 60% on legal fees (upcounsel.com)
- UpCounsel accepts only the top 5 percent of lawyers on its site. (upcounsel.com)
- As of 2020, personal bankers or tellers make an average of $32,620 per year, according to the BLS. (wgu.edu)
External Links
How To
How can Lean Manufacturing be done?
Lean Manufacturing techniques are used to reduce waste while increasing efficiency by using structured methods. They were developed in Japan by Toyota Motor Corporation (in the 1980s). The goal was to produce quality products at lower cost. Lean manufacturing emphasizes removing unnecessary steps from the production process. It consists of five basic elements: pull systems, continuous improvement, just-in-time, kaizen (continuous change), and 5S. Pull systems allow customers to get exactly what they want without having to do extra work. Continuous improvement means continuously improving on existing processes. Just-in-time is when components and other materials are delivered at their destination in a timely manner. Kaizen means continuous improvement. Kaizen involves making small changes and improving continuously. Five-S stands for sort. It is also the acronym for shine, standardize (standardize), and sustain. These five elements are combined to give you the best possible results.
Lean Production System
Six key concepts underlie the lean production system.
-
Flow - The focus is on moving information and material as close as possible to customers.
-
Value stream mapping: This is a way to break down each stage into separate tasks and create a flowchart for the entire process.
-
Five S's: Sort, Shine Standardize, Sustain, Set In Order, Shine and Shine
-
Kanban is a visual system that uses visual cues like stickers, colored tape or stickers to keep track and monitor inventory.
-
Theory of constraints: Identify bottlenecks and use lean tools such as kanban boards to eliminate them.
-
Just-intime - Order components and materials at your location right on the spot.
-
Continuous improvement - incremental improvements are made to the process, not a complete overhaul.