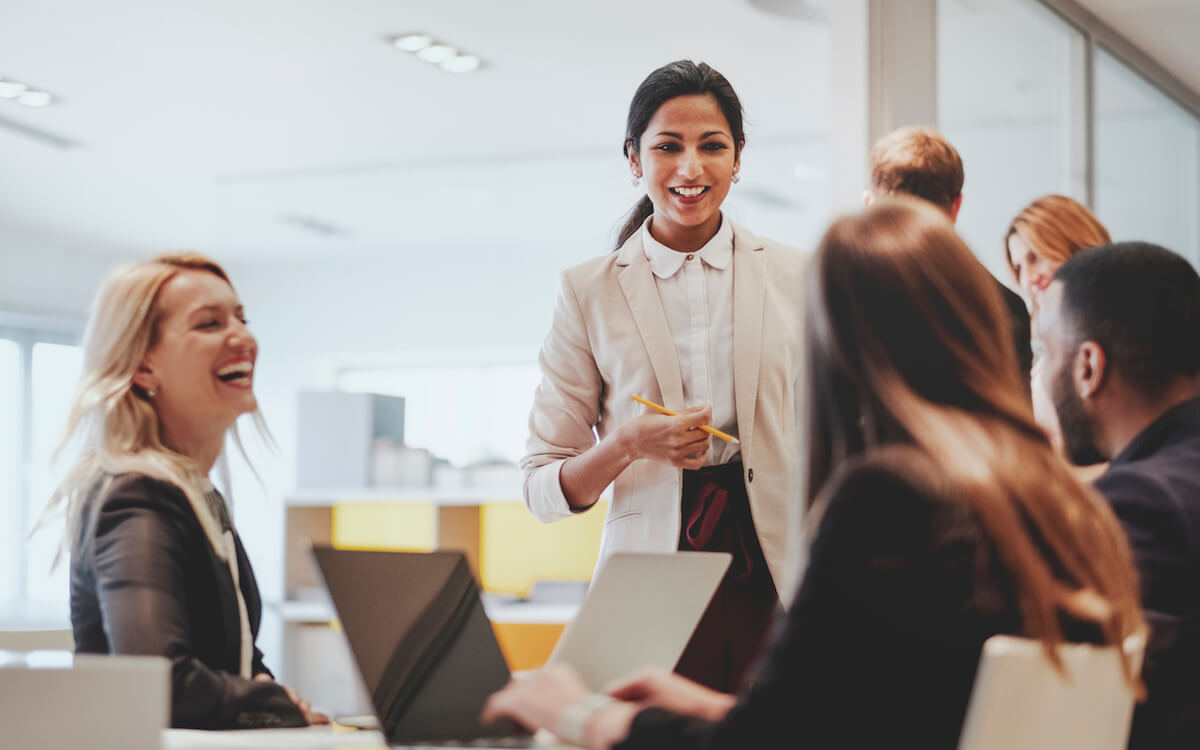
A capacity planning strategy must take into consideration the expected workload growth. It should also include any customer-driven growth. You should then plan accordingly. Here are four common scenarios to consider: Lead, Lag, Match, Adjustment. Each scenario presents different challenges and benefits. To ensure effective capacity planning, you need to consider all of these factors.
Lead strategy
Companies that have a leading strategy for capacity planning take an active role in increasing capacity and expanding the system before there is a demand. A lag strategy, however, waits for increased demand before expanding capacity. The advantage of a lead strategy is that it avoids the risk of running out of capacity due to an unexpected increase in demand.
You can use this strategy in many situations. However, it's most effective when the expected volume of goods and services is higher than anticipated. It can also be helpful when demand is high at times like the holidays. If a retailer hires seasonal workers in the holiday season, it can improve its workforce for greater traffic. The benefit of a leader strategy is that you can add more headcount quickly.
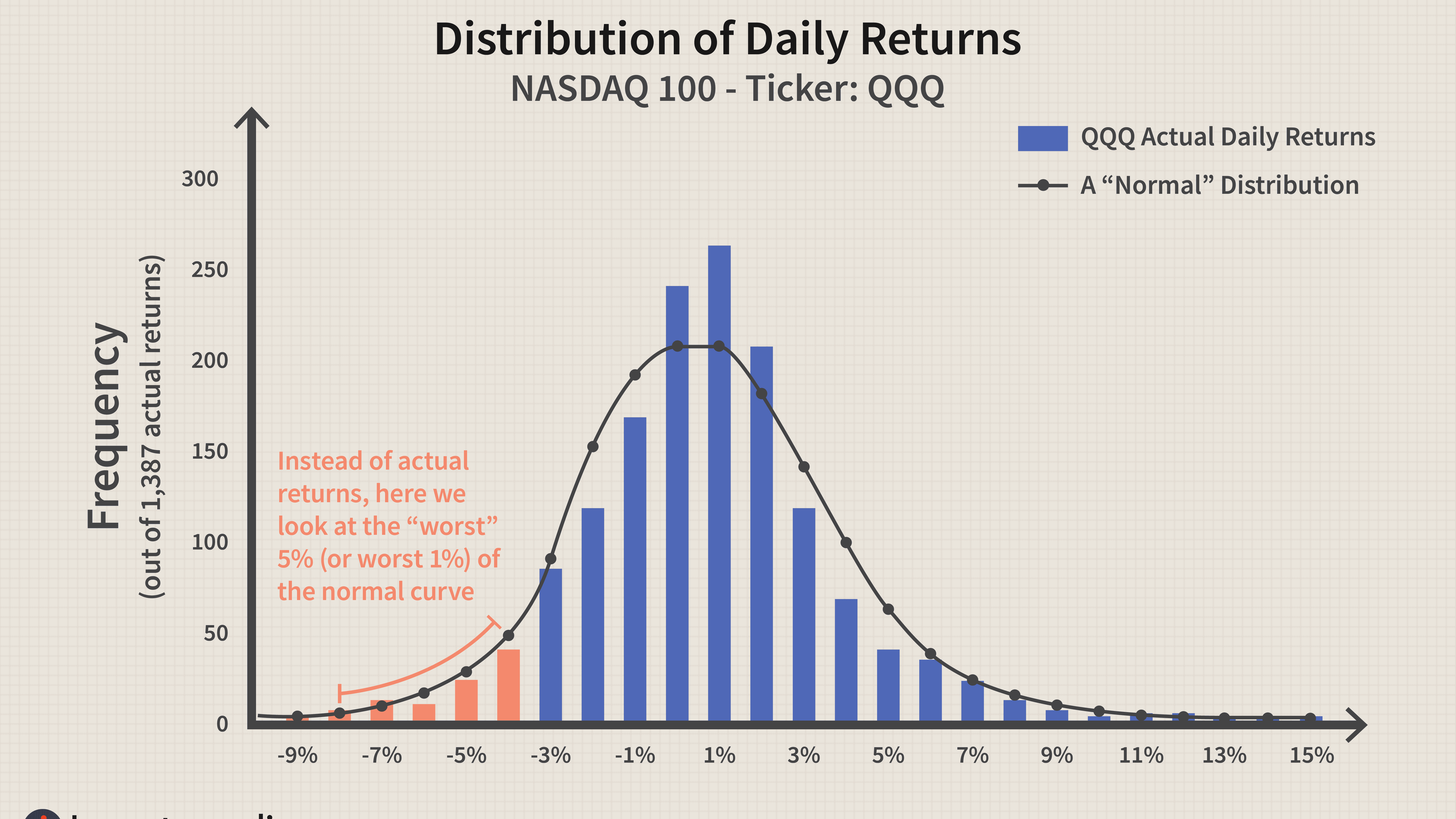
Lag strategy
To match capacity and demand, the Lag strategy for capacity plan is used. This strategy is much less risky than Lead, but requires more work and effort. It also tends to be more risk-averse than the other two strategies. The lead strategy on the other side tries to predict future demand, and then expand capacity accordingly. This strategy may not suit all organizations, due to limited resources or short time frames.
Companies with a stable business model will be able to choose a lag strategy. This strategy prevents excess inventory and waste by only increasing production when there is demand. But this method adds stress to the process of hiring and training new employees. An aggressive lead strategy is, however, more aggressive. It anticipates future demands and meets them before their time.
Match strategy
The Match strategy can be described as the middle ground between Lead and Lag strategies in capacity planning. It emphasizes incremental increases in capacity, rather than boosting demand ahead of time. Although it takes more planning and execution work, it is safer for most manufacturers. While increasing capacity can be expensive, it is less risky than either of the other options.
Match is a strategy that analyzes forecasts and monitors current demand. This allows the company quickly adapt to changing demand. While this strategy requires more work, it allows for swift and effective pivots. It streamlines operations by ensuring that resources are sufficient to meet future and current demands.
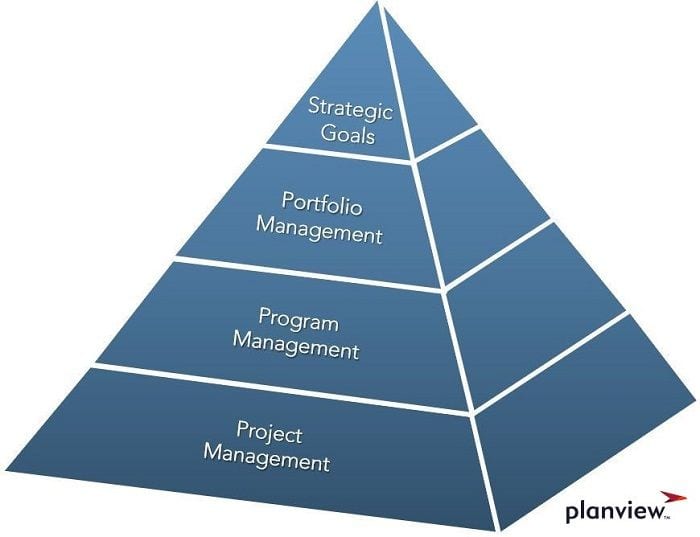
Adjustment strategy
The common approach to managing supply chain capacities is called the Adjustment strategy. This strategy ensures that supply chains are always available to meet demand. It allows businesses to scale their business and meet their obligations. The right strategy will increase your bottom line. The Adjustment strategy helps organizations better manage their supply chains.
This forces organizations to be realistic about their resources. Overestimating resources can reduce productivity and lead to lower worker morale. Over-allocating budgets can result in significant opportunity cost as they could be spent on continuous service improvement and innovation, employee pay, or employee wages. Moreover, this strategy forces leaders to become more realistic when they are forecasting their budgets.
FAQ
How can a manager motivate employees?
Motivation is the desire to do well.
It is possible to be motivated by doing something you enjoy.
You can also get motivated by seeing your contribution to the success or the improvement of the organization.
For example, if your goal is to become a physician, you will probably find it more motivational to see patients rather than to read a lot of medicine books.
The inner motivation is another type.
You may feel strongly that you are responsible to help others.
You might even enjoy the work.
Ask yourself why you aren't feeling motivated.
You can then think of ways to improve your motivation.
How does Six Sigma work?
Six Sigma uses statistical analysis to find problems, measure them, analyze root causes, correct problems, and learn from experience.
The first step to solving the problem is to identify it.
The next step is to collect data and analyze it in order to identify trends or patterns.
The problem can then be fixed by taking corrective measures.
Finally, data will be reanalyzed to determine if there is an issue.
This continues until the problem has been solved.
What are the five management steps?
Each business has five stages: planning, execution and monitoring.
Setting goals for the future is part of planning. Planning involves defining your goals and how to get there.
Execution takes place when you actually implement the plans. It is important to ensure that everyone follows the plans.
Monitoring is the act of monitoring your progress towards achieving your targets. Regular reviews of performance against budgets and targets should be part of this process.
Every year, there are reviews. They give you an opportunity to review the year and assess how it went. If not there are changes that can be made to improve the performance next year.
After the annual review, evaluation takes place. It helps to identify what went well and what didn’t. It also provides feedback on the performance of people.
What are the steps in the decision-making process in management?
Managers face complex and multifaceted decision-making challenges. It involves many factors, including but not limited to analysis, strategy, planning, implementation, measurement, evaluation, feedback, etc.
The key thing to remember when managing people is that they are human beings just as you are and therefore make mistakes. There is always room to improve, especially if your first priority is to yourself.
This video will explain how decision-making works in Management. We discuss different types of decisions as well as why they are important and how managers can navigate them. These topics are covered in this course:
What is the difference between TQM and Six Sigma?
The main difference between these two quality-management tools is that six-sigma concentrates on eliminating defects while total QM (TQM), focuses upon improving processes and reducing expenses.
Six Sigma is an approach for continuous improvement. It emphasizes the elimination of defects by using statistical methods such as control charts, p-charts, and Pareto analysis.
This method seeks to decrease variation in product output. This is accomplished through identifying and correcting root causes.
Total Quality Management involves monitoring and measuring every aspect of the organization. This includes training employees to improve their performance.
It is frequently used as an approach to increasing productivity.
Statistics
- Hire the top business lawyers and save up to 60% on legal fees (upcounsel.com)
- The average salary for financial advisors in 2021 is around $60,000 per year, with the top 10% of the profession making more than $111,000 per year. (wgu.edu)
- As of 2020, personal bankers or tellers make an average of $32,620 per year, according to the BLS. (wgu.edu)
- Our program is 100% engineered for your success. (online.uc.edu)
- 100% of the courses are offered online, and no campus visits are required — a big time-saver for you. (online.uc.edu)
External Links
How To
How can you create a Quality Management Plan, (QMP)?
QMP (Quality Management Plan) is a system to improve products and services by implementing continuous improvement. It emphasizes on how to continuously measure, analyze, control, and improve processes, product/service, and customer satisfaction.
QMP stands for Quality Management Process. It is used to guarantee good business performance. QMP helps improve production, service delivery and customer relationships. A QMP should include all three aspects - Processes, Products, and Services. The QMP that only addresses one aspect of the process is called a Process QMP. QMPs that focus on a Product/Service are known as "Product" QMPs. And when the QMP concentrates on Customer Relationships, it is called "Customer" QMP.
When implementing a QMP, there are two main elements: Scope and Strategy. They can be described as follows:
Scope: This defines what the QMP will cover and its duration. This scope can be used to determine activities for the first six-months of implementation of a QMP in your company.
Strategy: This describes how you will achieve the goals in your scope.
A typical QMP consists of 5 phases: Planning, Design, Development, Implementation, and Maintenance. Below is a description of each phase:
Planning: This stage identifies and prioritizes the QMP's objectives. In order to fully understand and meet the needs of all stakeholders involved in this project, they are consulted. Once the objectives and priorities have been identified, it is time to plan the strategy to achieve them.
Design: The design stage involves the development of vision, mission strategies, tactics, and strategies that will allow for successful implementation. These strategies are implemented by the development of detailed plans and procedures.
Development: Here, the development team works towards building the necessary capabilities and resources to support the implementation of the QMP successfully.
Implementation involves the actual implementation using the planned strategies.
Maintenance: Maintaining the QMP over time is an ongoing effort.
In addition, several additional items must be included in the QMP:
Participation of Stakeholders: The QMP's success depends on the participation of stakeholders. They need to be actively involved in the planning, design, development, implementation, and maintenance stages of the QMP.
Project Initiation: The initiation of any project requires a clear understanding of the problem statement and the solution. Also, the initiator should understand why they are doing it and what they expect.
Time Frame: It is important to consider the QMP's time frame. You can use a simplified version if you are only going to be using the QMP for short periods. If you are looking for a longer-term commitment, however, you might need more complex versions.
Cost Estimation. Cost estimation is another crucial component of QMP. Without knowing how much you will spend, planning is impossible. Before you start the QMP, it is important to estimate your costs.
QMPs should not be considered a static document. It can change as the company grows or changes. So, it should be reviewed periodically to make sure that it still meets the needs of the organization.